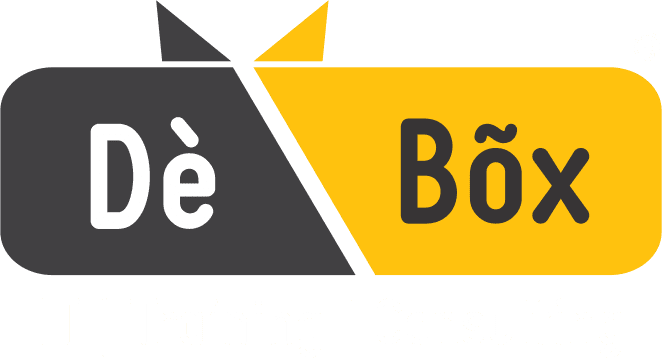
Apparel ERP is developed by continuous research and constant innovation to automate the apparel manufacturing process without changing their business practices.
Simplifying the most challenging and complex tasks keeping in mind their system proficiencies and minimizing their tasks by proving simple solutions.
Professional, Trained and Systematic customer service team working on quick response time to provide the best after sales service.
Visual Dashboards for different roles making it simple to analyze data
Process bucketing of all Styles to know the Birds Eye View across all the factories
To Do List of each user based on processes and tasks assigned to the user
Also view Dashboard of the team under the user
Coffee Table Dashboard Report emailed every morning to the Senior Management (Customized
Admin / Senior Management can send messages / instructions / notifications to all the users division wise
Messages can be scheduled to go on a particular date for the defined set of users
Send product/order related messages directly from within ERP
Messages can also be sent to an individual user by Admin / Senior Management
Email integration with Apparel ERP helps in seamless communication
It reduces dependence on email systems like outlook etc.
Automatically organizes emails under relevant Styles which makes it easier to have all communication at one place
Style wise separate communication tabs for Internal, Buyer, Supplier and Vendor Communication
Create Style directly from Buyer’s email and attach Tec pack to the Style automatically
Complete PD Workflow from Buyer Tec pack to Proto Sample and Style Costing
The module includes material, cost and vendor finalization
Approval Matrix for every process
Turnaround time tracking for each user compared to standard allocated time
Internal assignments to purchase team for costing of articles
Supplier communication templates for easy and fast process
Import Pattern from third party system and Fabric Consumption analysis by markers
Multiple versions of Material Cost and Cost Estimate Sheet can be maintained in the ERP
Buyer Purchase Order import facility in Apparel ERP
Role & right based viewing of the Buyer Purchase Order in Style
Color and Size wise quantities of the Style visible to Planning and Merchandizing
Multiple Destinations Purchase Order
Quick View to Customers Credit/Outstanding Payments
Share Product Purchase Orders and Specs online with suppliers in preset templates
Collaborate with suppliers online and make them part of your Time & Action plan
Suppliers can directly Input Advanced Shipment Notices (ASNs) and upload invoice
Complete module for Vendor Evaluation for PD/Production Outsourcing
Style wise Vendor Communication with pre-defined templates
Outsourced Vendor Rate Comparison by ERP
Purchase Order Generation for the finalized Vendors through Predefined templates